Within the field of robotics, articulated robots are particularly flexible, versatile, and precise. These multi-jointed robots are made to replicate the range of motion of a human arm, therefore enabling their amazing accuracy and adaptability in task performance. Designed for delicate operations, welding metal parts, or assembly of complex components, articulated robots are leading edge in automation.
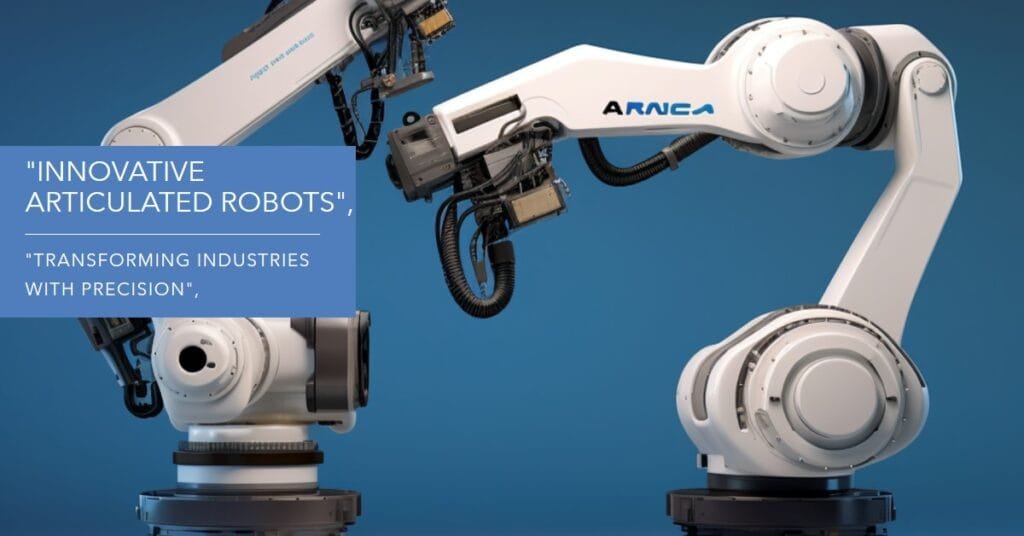
In industrial, automotive, aerospace, and healthcare as well as other sectors, articulated robots are indispensable. Their numerous direction and angle mobility makes them valuable in applications requiring great repeatability, speed, and accuracy. By increasing operational efficiency, lower labor costs, and better safety, these robots have changed manufacturing lines. With their sophisticated skills, articulated robots are not only raising output but also changing the manner that work is completed all around.
These robots are meant to manage difficult and repetitious duties, therefore freeing human workers to concentrate on more strategic and artistic work. This produces improved product quality, a more efficient workflow, and a general enhancement of the workplace surroundings. Speaking robots are leading the way as automation develops and guiding sectors toward a smarter, more efficient future.
This blog will go into great detail on what articulated robots are, investigate their main characteristics, look at their many uses, and underline how these robots are revolutionizing several industries. Knowing their influence helps us to value the part articulated robots play in transforming automation.
What Are Articulated Robots?
Definition of Articulated Robots
Usually featuring numerous joints, articulated robots are robotic devices modeled on the structure and movement of a human arm. Because of their exact motors and sensors, these robots can carry out a great variety of jobs with great efficiency and accuracy. Industries requiring complex motions, including manufacturing, assembly, and even surgical operations, find great use for them.
Key Features
Their several joints—usually between six and seven—that provide them great flexibility and adaptability set articulated robots apart. These joints enable the robot to rotate, stretch, and move in several directions, therefore enabling its capacity to complete difficult jobs. What distinguishes articulated robots from other robotic systems is their capacity for precise object manipulation together with a great range of motion. Their adaptability also makes them perfect for functioning in limited or dynamic surroundings.
History of Articulated Robots
The history of articulated robots is characterised by the early industrial automation of the mid-1900s. Like Unimate in the 1960s, the initial industrial robots were intended for straightforward repetitive chores like material handling and welding. Advances in computation, artificial intelligence, and robotics technology throughout time allowed these systems to develop into the very sophisticated articulated robots we know today. From automobile manufacturing to medical operations, articulated robots are employed in a variety of sectors today, highlighting the amazing development from early industrial robots to the flexible machines they are now.
Types of Articulated Robots
6-Axis Robots
These very flexible robots for a variety of industrial applications have six degrees of freedom. The six axes let one move in all directions—linear and rotational—that guarantees exact positioning and intricate operations. Common uses are material handling, painting, welding, and assembling; where accuracy and flexibility are especially important. Their flexibility makes them a mainstay in sectors including electronics manufacture and automotive engineering.
7-Axis Robots
Comparatively to their 6-axis predecessors, 7-axis robots provide even more flexibility and mobility with an extra axis. These robots can reach around barriers or complete jobs in limited areas because to their increased degree of flexibility. For handling big or oddly shaped things, its design is quite helpful; hence, it is perfect for sectors like manufacturing of aerospace or medical equipment that need careful handling.
Heavy-Duty Articulated Robots
Designed for robustness and longevity, these robots can operate in demanding conditions and carry large weights. They shine in uses like automotive manufacture, where they lift and place car parts, and heavy machinery handling in sectors like shipbuilding or construction, with strong structures and powerful engines. Their indispensible nature for heavy-duty jobs stems from their capacity to operate under demanding situations.
How Articulated Robots Work
Joint Structure and Degrees of Freedom
Multiple joints in articulated robots allow each one to offer some degree of freedom (DOF). These degrees let the robot replicate human arm motions by moving in either linear or rotational directions. With six joints, for instance, a 6-axis robot may reach any point within its workspace and complete complex jobs including assembly or welding. For industrial uses, DOF’s combination of exact control and wide range of motion lets you be flexible.
Coordination of Movement
Coordination of the movement of an articulated robot’s joints depends critically on its control system. The system determines the best path and speed for every joint using algorithms so that it may precisely complete a job. In jobs like pick-and-place or painting, the control system guarantees coordinated and fluid movements, so reducing mistakes and raising productivity. Inverse kinematics and advanced kinematics enable difficult motions.
Sensors and Vision Systems
Sensors and visual systems built into modern articulated robots improve their precision and adaptability. By means of real-time feedback on position, force, and proximity, sensors help the robot dynamically modify its motions. Vision systems—which include cameras and artificial intelligence-based recognition software—let robots recognize objects, avoid hazards, and change with the times. Particularly in uses like quality checking or handling delicate components, these technologies guarantee great precision.
Applications of Articulated Robots
Manufacturing and Assembly
Manufacturing uses articulated robots widely for jobs including assembly, part handling, packaging, and welding. In sectors including automotive, electronics, and consumer goods, their speed and accuracy make them very vital. For instance, they regularly precisely weld vehicle chassis or assemble complex electrical components.
Industrial Welding and Painting
In spray painting and welding, articulated robots shine in guaranteeing consistency and accuracy. In the automotive and aerospace sectors, they can manage repetitive operations and produce excellent outcomes with less human contact to dangerous surroundings.
Material Handling and Palletizing
These robots quickly move, sort, and arrange goods in warehouse automation and logistics. In food processing and e-commerce, they palletize products to boost output and cut manual labor.
Medical and Surgical Applications
With their exact and regulated motions, which improve surgical results, articulated robots help in operations. They also find application in the production of medical devices, guaranteeing careful handling of sensitive components in sectors of healthcare.
Packaging and Sorting
Robots load goods into boxes or sort items on manufacturing lines, therefore simplifying packing and sorting procedures. In food, beverage, and e-commerce sectors, they are extensively applied to effectively manage enormous product volumes.
Benefits of Articulated Robots
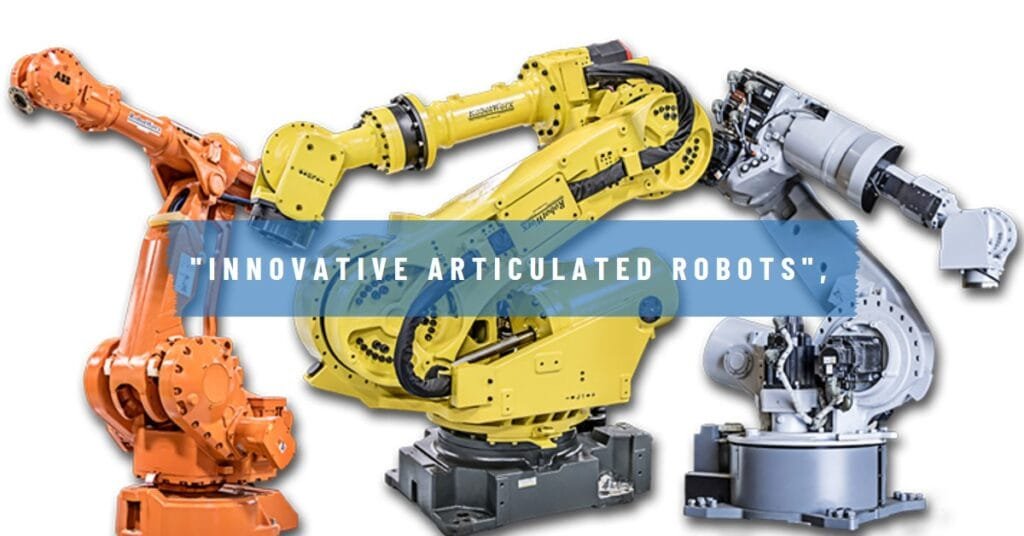
Flexibility and Precision: Articulated robots shine in precisely completing complex jobs in limited areas. Their multi-axis movement makes them flexible to meet different industrial needs since it allows a great range of operations from delicate assembly to exact welding.
Increased Productivity: These always running robots greatly increase manufacturing consistency and speed as they are not tired. Automating monotonous jobs lets human employees concentrate on more valuable work, hence improving general productivity.
Cost Efficiency: Although the initial outlay in robotic systems might be significant, articulated robots save long-term costs by lowering labor costs and mistake minimization. Their dependability makes production quality better and reduces waste, thereby offering a good return on investment.
Enhanced Safety: By undertaking dangerous duties like handling toxic chemicals, welding, or heavy lifting, articulated robots help to lower the risk of injury. This keeps operating efficiency while making the surroundings safer for human employees.
Scalability: As companies expand, articulated robots fit very well with current manufacturing lines. Their modular architecture and programmable character enable easy addition of new units or reconfiguration for different purposes, therefore aiding scalability and adaptability in dynamic sectors.
Challenges of Articulated Robots
High Initial Cost: Including the cost of the robot itself, installation, and integration into current systems, articulated robots have a significant upfront outlay. Although they save long-term, smaller companies may find the first outlay difficult.
Maintenance and Repairs: articulated robots need constant maintenance if we are to guarantee their performance. This covers lubrication, cleaning, and replacement of worn-out components. Unexpected breakdowns might cause problems and result in further repairs.
Need for Skilled Labor: Using and controlling articulated robots calls for experienced operators and specialists. As technologies develop, these experts must be taught in programming, debugging, and maintaining robotic systems, which can raise labor costs and need for continual education.
Space Requirements: Enough room is required for articulated robots to operate safely and with range of motion. Accommodating these robots in small spaces can be difficult and calls for careful planning and maybe expensive redesign of current layouts.
Future Trends in Articulated Robotics
Artificial Intelligence Integration: Including artificial intelligence into articulated robots improves their capacity for decision-making, learning from prior activities, and environment adaptation. This lets robots accomplish difficult tasks with more efficiency and autonomy.
Collaborative Robots (Cobots): Designed to operate securely adjacent to humans, cobots mark the next phase in robotics. These robots are perfect for sectors giving human-robot cooperation since they have sophisticated sensors and programming to guarantee safe contact in shared workplaces.
Advanced Sensors and Vision Systems: By means of advanced sensors and visual systems, robots can identify objects, avoid obstacles, and precisely interact with their environment. These developments raise performance standards for jobs including quality control, sorting, and assembly.
Human-Robot Collaboration: Easy human-robot cooperation is the emphasis of future trends. Teams in manufacturing, healthcare, and logistics may maximize efficiency and creativity by fusing human intuition with robotic accuracy.
Energy Efficiency and Sustainability: In robotics development, utilization of sustainable materials and energy-efficient designs are starting to take front stage. These developments minimise environmental effect and save running expenses, therefore complementing world sustainability objectives.
Real-World Examples of Articulated Robots in Action
Automotive Manufacturing
A pillar of automobile manufacturing lines are articulated robots. Using these robots for jobs like welding car chassis, painting exteriors, and component assembly, companies like Ford and Tesla Their accuracy and speed increase output while preserving quality.
FANUC and ABB Robotics
Among industry leaders in articulated robots are FANUC and ABB. ABB’s robots shine in welding and painting; FANUC’s robots are extensively applied in manufacturing for material handling and assembly. These firms keep innovating and establish standards for robotics technology.
Medical Robotics
In the medical field, articulated robots like as the da Vinci Surgical System help to facilitate minimally invasive procedures. These robots improve surgical results by giving surgeons more accuracy and control, hence lowering patient recovery times.
Amazon Fulfillment Centers
At its warehouses, Amazon deploys articulated robots to automate material handling. These robots guarantee speedier delivery times by sorting, moving, and packing goods, so simplifying processes. Their combination shows how flexible articulated robots are in logistics.
Articulated Robot Arm
One kind of robotic system with rotating joints that lets it replicate human arm motions is an articulated robot arm. These joints give several degrees of flexibility, hence the arm is quite flexible and competent to complete difficult jobs. Because of their accuracy, adaptability, and efficiency, articulated robot arms are frequently seen in manufacturing, healthcare, and logistics.
Key Features:
- Degrees of Freedom: Usually spanning 4 to 7 axes, they allow a great spectrum of motion.
- Versatility: Fit for jobs including painting, assembling, material handling, welding, and even surgery.
- Precision: high accuracy in repetitious work helps to lower manufacturing mistakes.
- Payload Capacity: Based on the design, can manage lightweight to heavy-duty operations.
Applications:
- Industrial Automation: Found in palletizing, welding, and assembly processes.
- Healthcare: helps with rehabilitation and surgery.
- Research and Development: for lab experiments and testing.
Leading makers of articulated robot arms are ABB, FANUC, Kuka, and Universal Robots. More suited to current automation requirements, these systems are developing with AI integration, cooperative functionality, and improved sensors.
Conclusion
With their unequaled flexibility, precision, and speed, articulated robots have transformed the field of automation. Their indispensible nature stems from their capacity to complete challenging jobs spanning several sectors, from automotive manufacture to healthcare. By managing hazardous or repetitious activities, these robots not only increase output but also worker safety.
Innovations include artificial intelligence, cooperative robotics, and energy-efficient designs will progressively extend the possibilities of articulated robots as technology develops. Companies implementing these ideas now are setting themselves up for an automated and more effective future.
Said robots are a game-changing investment if you want to simplify processes, cut expenses, and increase output. Discover how they might change your company’s processes and enable you to remain competitive in the always changing scene of technology. Begin your path towards better, more effective systems right now!
Frequently Asked Questions (FAQs)
1. What are the main advantages of articulated robots over other types of robots?
Because of their several axes of movement, articulated robots provide great flexibility and precision. For jobs needing a great degree of accuracy, such welding, assembly, and painting, they are perfect as they can handle difficult tasks in confined areas.
2. Can articulated robots work alongside humans?
Because of their several axes of movement, articulated robots provide great flexibility and precision. For jobs needing a great degree of accuracy, such welding, assembly, and painting, they are perfect as they can handle difficult tasks in confined areas.
3. What industries benefit most from using articulated robots?
Industries include automotive manufacture, electronics, aerospace, healthcare, and logistics gain greatly as well. In jobs like assembly, welding, material handling, and surgery, these robots increase accuracy, efficiency, and safety.
4. How much does an articulated robot cost?
An articulated robot’s cost will vary greatly based on its size, degree of capability, and use. While complex systems for industrial use can top $100,000, entry-level ones might begin at $25,000.
5. How do articulated robots increase efficiency in manufacturing?
Working constantly without tiredness, articulated robots guarantee constant quality and faster manufacturing rates. Their streamlining of processes and reduction of human mistakes greatly increase general manufacturing efficiency.