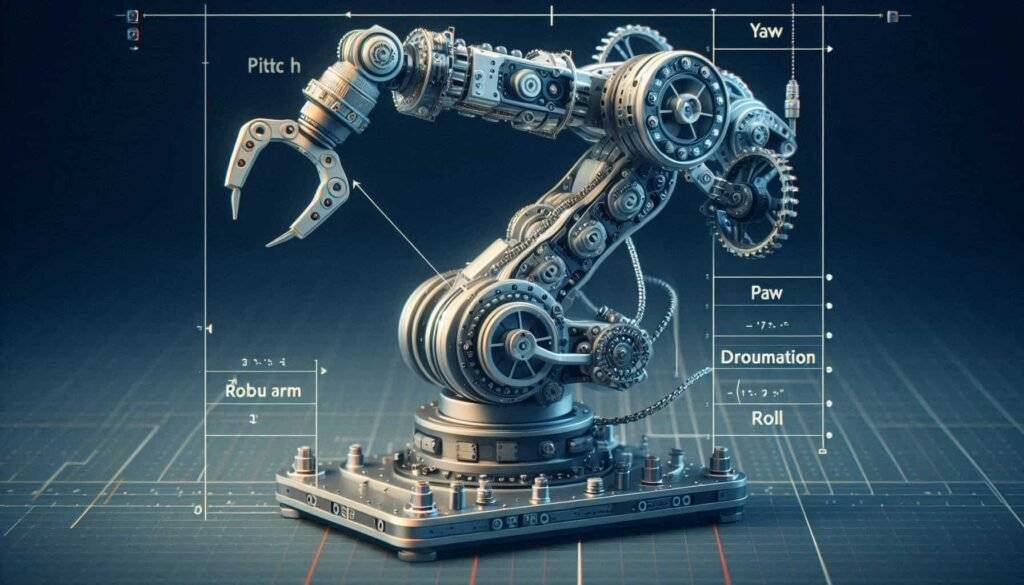
Leading modern robotics and automation are robot arms, which find use in everything from industry to healthcare. One must first grasp the main motions these robotic arms produce if one is to really grasp their operation. Robot arm pitch yaw and roll operate complex jobs with accuracy on a basis derived from pitch, yaw, and roll movements. We shall explore thoroughly in this paper what these movements are, how they cooperate, and their significance for the direction of robotics.
Overview of Robot Arms in Robotics
Designed to mimic human arm motions, robot arms let machines complete activities otherwise requiring human strength and dexterity. Their many directional movement is made possible by several joints and actuators included into their construction. For procedures like assembly, material handling, and even surgery, these movements along with force application make robot arms indispensable. Unlocking the full potential of a robot arm depends on knowing its fundamental mechanics—especially those related to mobility.
Importance of Understanding Pitch, Yaw, and Roll in Robot Arm Movements
Robot arm pitch yaw and roll are common robotics words used to characterize rotational motions allowing a robot arm to reach, handle, or rotate things. These motions specify the interaction of the robot arm with its surroundings. Achieving high-performance levels in both industrial and service robotics depends on pitch, yaw, and roll whether it is rotating an object, picking it up, or accurately orienting it.
What is Pitch, Yaw, and Roll?
Defining Pitch, Yaw, and Roll
Originally adopted from mechanical engineering and aviation, pitch, yaw, and roll characterize the rotation of an object in three- dimensional space. Robotic arm orientation is controlled in part by these motions.
- Pitch Pitch is the upward or downward slope of the arm as a result of rotation around a horizontal axis.
- Yaw is the arm side to side movement around a vertical axis.
- Roll refers to the twisting left or right by means of a rotation along the longitudinal axis of the robot arm.
These three motions let robot arms to be versatile, able of exact and dynamic motions in many environments.
How These Terms Apply to Robotics
Understanding pitch, yaw, and roll enables engineers and operators designing and programming the arm for a variety of applications in robotic systems. In an industrial robot, for instance, pitch might regulate tool lifting and lowering, yaw might change its angle to match a target, and roll could turn the tool for minute changes.
The Role of Pitch in Robot Arm Motion
Understanding Pitch
Pitch is the robot arm moving along a horizontal axis either up or down. We bend our heads to view something higher or lower, hence this is similar. Pitch enables a robot arm to reach targets at different heights, which is crucial for assembly, inspection, or any job requiring vertical orientation.
Application of Pitch in Robot Arms
Pitch movement is essential in uses requiring height alterations. In the automotive sector, for instance, a robot arm might pick up a car part from a conveyor belt and move it vertically to position it correctly in assembly. Pitch in medical robotics lets the arm change the angle of a surgical tool to access different body parts.
Yaw: Its Impact on Robotic Arm Operations
What is Yaw?
Yaw is rotation around a vertical axis. This maneuver lets the robot arm swing horizontally. You are yaw if you picture stillness and left or right turning of your body.
How Yaw Affects Robotic Arm Navigation
The robot arm’s orientation in space is made possible in great part by yaw. Yaw helps a robot arm in automated manufacturing lines to change its position such that it may pick up an object, relocate it, or orient it in a specific direction. For jobs requiring exact placement, including screw installation or fitting an item into a confined area, it is absolutely vital.
Roll: The Unsung Hero of Robotic Motion
Defining Roll in the Context of Robotics
Roll describes the robot arm’s rotation along its length, therefore twisting the arm around its axis. Although pitch and yaw take front stage, this movement is quite important for some jobs requiring exact control.
How Roll Influences the Functionality of Robot Arms
When a robot arm must rotate or change the orientation of an object in its grasp, roll is crucial. In a robotic welding system, for instance, the arm might have to roll to guarantee proper relative location of the welding torch to the workpiece. Roll similarly helps the robot arm align tools to the proper angle in jobs like screwing or drilling.
How Robot Arms Utilize Pitch, Yaw, and Roll Together
Integration of All Three Movements
Although pitch, yaw, and roll have individual value, the ability to combine these three motions is where a robot arm truly has strength. Coordinating all three axes of rotation helps a robot arm to accomplish difficult jobs with amazing accuracy.
Examples of Coordinated Pitch, Yaw, and Roll in Action
Imagine a manufacturing robot arm building an electronic item. The arm could first lower to grab a component. It next moves horizontally toward its assembly station using yaw. Before putting the component in the gadget, the arm could finally roll to twist and properly position it. This mix of actions guarantees precision and effectiveness in the production line.
Types of Robot Arms: Cartesian, SCARA, and More
Overview of Robot Arm Types
Different jobs are intended for each of the numerous kinds of robot arms. Among the most often occurring ones are:
- Cartesian Robots: Well suited for pick-and-place tasks, these arms travel in straight lines along three axes (X, Y, and Z). They can still use pitch, yaw, and roll to a degree even if they might not be as flexible as other varieties.
- SCARA Robots: These arms can do assembly and packaging and are made for fast, exact motions. Pitch, yaw, and roll allow SCARA robots to maximize manipulation and positioning.
- Articulated Robots: These are the most flexible robot arms since their several joints let them rotate freely in all directions. Articulated robots shine at difficult jobs needing the mix of pitch, yaw, and roll.
How Different Types Handle Pitch, Yaw, and Roll
Every kind of robot arm addresses these motions differently. Cartesian robots, for instance, usually concentrate on linear motion and change position using pitch and yaw. Conversely, SCARA and articulated robots are meant to offer more freedom and easy handling of all three motions.
Applications of Pitch, Yaw, and Roll in Industrial Robotics
Common Industrial Uses
Precision is mostly relied upon in industrial robots; so, pitch, yaw, and roll are absolutely essential for the required precision. Jobs including assembly, material handling, welding, and even packaging call for these motions.
To pick up a part, for example, a robot arm might pitch and yaw then roll to place the part in the right orientation for assembly. Maximizing efficiency and guaranteeing high-quality output depend on these motions.
How Precision in Pitch, Yaw, and Roll Improves Efficiency
High precision movement of robot arms lowers the possibility of mistakes and rework, therefore improving output. Robotic systems can faster and more precisely handle difficult jobs than human workers by adjusting pitch, yaw, and roll.
How to Control Pitch, Yaw, and Roll in Robotic Systems
Overview of Control Systems
Pitch, yaw, and roll control calls for complex systems. Usually driven by algorithms calculating the required joint angles to reach the intended motions, these systems Two common approaches of control are forward and inverse kinematics.
Controllers and Algorithms Used to Manage Movement
To change their motions, robotic arms use PID controllers—proportional, integral, derivative—among other controllers. These controllers guarantee that the arm reacts precisely to commands and movements naturally. Furthermore, depending on its tasks and the surroundings, software algorithms determine the best pathways for the actions of the robot arm.
Sensors and Feedback Systems for Pitch, Yaw, and Roll
Role of Sensors in Ensuring Accuracy
Accurate motions of the robot arm depend critically on sensors. These sensors maintain exact control by means of real-time data on the position and orientation of the arm, which helps to remedy any errors.
Types of Sensors Used in Robot Arms
Robot arms feature encoders, gyroscopes, and accelerometers among their common sensors. Accelerometers measure the forces acting on the arm; gyroscopes track arm orientation; encoders track arm joint movement.
Challenges in Managing Pitch, Yaw, and Roll
Common Issues Faced in Robot Arm Movements
Pitch, yaw, and roll can be difficult even with technological developments. Movement can be erroneous from mechanical wear and tear, sensor flaws, and joint misalignment.
Solutions to Improve Precision
Engineers constantly upgrade calibration methods, apply cutting-edge sensors, and create improved software algorithms capable of real-time error compensation in order to meet these problems.
Advancements in Robotic Arm Motion Control
New Technologies Impacting Pitch, Yaw, and Roll
More complex control of pitch, yaw, and roll is made possible by recent advances in artificial intelligence and machine learning. These technologies let robot arms more successfully adapt to new tasks and surroundings.
The Future of Robotic Motion
Robotic arms should get increasingly more flexible and accurate going forward. From surgery to space exploration, these arms will be able to manage ever challenging chores because to developments in artificial intelligence and sensor technologies.
Pitch, Yaw, and Roll in Robotics Simulation
The Role of Simulation Software in Training and Design
Designing novel motions and training robotic systems depends on simulation programs. Before the robot arm is turned on, engineers can maximize its motions by modeling pitch, yaw, and roll.
How Simulations Help Optimize Motion
Simulations give engineers important new perspectives on how various movements will interact and enable them to adjust control systems for optimal performance.
The Impact of Pitch, Yaw, and Roll on Robot Arm Performance
How Movement Accuracy Affects Performance
Direct effects on a robot arm’s performance are accuracy in pitch, yaw, and roll. More exact motions produce faster, more effective operations that reduces mistakes and produces better results.
Real-World Examples of Performance Improvement
Robots with ideal pitch, yaw, and roll motions greatly outperform human labor in industrial applications, thereby saving time on jobs and raising general output.
Conclusion
Fundamental motions in robotics that let robot arms complete difficult jobs with great accuracy include pitch, yaw, and roll. Particularly in industrial uses, the ongoing development of robotics depends on an awareness of and control for these movements. These movements should becoming much more exact and flexible as technology develops, therefore creating fresh opportunities for automation in many other fields.
FAQs
What is the difference between pitch, yaw, and roll in robotics?
Pitch, yaw, and roll characterize the three rotating motions a robot arm can produce: pitch moves the arm up and down, yaw moves it side to side, and roll spins the arm along its length.
Why is precision in robot arm movement important?
In both industrial and service sectors, accuracy of tasks depends on precision, which also helps to lower mistakes and improve productivity.
How do sensors help in controlling robotic arm movements?
To keep accuracy, sensors give real-time data on the position and orientation of the robot arm, therefore guiding its motions.
What are some common challenges in robot arm motion control?
Joint misalignment, sensor errors, mechanical wear—all of which might compromise the arm’s capacity for exact movement—are among the challenges.
What future advancements could change the way we control robot arms?
Sensor technology, artificial intelligence, and machine learning will keep enhancing the accuracy and adaptability of robotic arms, hence enabling their ability to carry out increasingly difficult jobs with more efficiency.